La parole est
à Philippe Moniotte, pour un article qu´il a bien voulu écrire
pour nous après qu´un enrichissant échange de points
de vue sur cette technique a eu lieu sur la liste Ptitrain |
|
|
 |
Le
moulage en résine |
Avant-propos. Cet article n´est
que la relation de l´expérience de l´auteur, qui n´a pas la prétention d´avoir exploré
le sujet dans ses moindres recoins. Les techniques exposées ne sont certes pas l´unique vérité
dans le domaine du moulage amateur, mais simplement l´histoire d´une approche qui a donné des résultats
acceptables ou du moins, j´espère que le lecteur en jugera ainsi. P.M.
 |
Une caisse de locomotive diesel, réalisée en résine
|
Peut-être est-ce paradoxal, mais j´ai choisi à
l´époque de faire mes premières armes sur un moulage assez complexe. Une caisse de locomotive, moulée
d´une pièce, requiert un moule en deux parties et pose des problèmes de coulée. C´est
évidemment aussi ce qui fait le possible intérêt de cet article. Qui peut le plus peut le moins,
dit-on.
Le moule est réalisé en caoutchouc silicone bicomposant
vulcanisable à froid (RTV, pour les techniciens). Ce caoutchouc se présente sous la forme d´un sirop
très visqueux. On lui ajoute une petite quantité de catalyseur, qui va induire en quelques dizaines de minutes
une réaction de solidification, appelée vulcanisation. Dans ce cas particulier, la vulcanisation se produit
à température ambiante, mais elle sera accélérée si on chauffe quelque peu le système.
La base chimique du silicone de moulage est essentiellement
la même que celle des mastics du même nom, avec lesquels on réalise des joints de sanitaires, par exemple.
Notre silicone comporte cependant trois différences qui le rendent propre au rôle que nous en attendons :
il est moins visqueux et flue sous son propre poids, si bien qu´on peut le couler autour
d´un modèle maître. Il est formulé pour ne pas adhérer, ce
qui permet de démouler le modèle maître sans difficultés. Il fait prise sans intervention des
agents atmosphériques (humidité ou oxygène) qui détermine la solidification de son cousin des
salles de bain ; cette dernière caractéristique lui permet de durcir de manière homogène
dans toute son épaisseur.
Notons qu´il est toutefois possible de réaliser
de tout petits moules au moyen de mastic en tube, a condition de prévoir sur le modèle-maître un agent
de démoulage efficace, tel que la paraffine. Mais c´est un pis-aller qui rencontre vite ses limites.
 Le
moule terminé est généralement très souple, ce qui permet de démouler des contre-dépouilles
relativement importantes. Il est cependant fortement conseillé de limiter ces dernières autant que possible,
car les fortes déformations fatiguent le moule : le défaut fondamental des caoutchoucs silicones, quels
qu´ils soient, est leur assez mauvaise résistance au déchirement. Les variétés de caoutchoucs
les plus dures sont aussi les plus résistantes à cet égard, mais c´est aux dépens de
la facilité de démoulage, cela va sans dire.
La formulation de ces caoutchoucs ne supporte pas l´à-peu-près.
Il est impératif, si l´on veut tirer le maximum d´un moule, de respecter à la lettre le mode
d´emploi. C´est beaucoup plus important ici que pour les résines bicomposant, par exemple, qui sont
plus accommodantes au niveau des proportions.
Quelques recommandations (croyez-en quelqu´un qui l´a
appris à ses dépens !). Il faut :
1 Mesurer
méticuleusement les quantités des deux composants. Par la nature de la réaction, un excès ou
un défaut de catalyseur donnent en un moule plus fragile au déchirement et au vieillissement prématuré.
2 Mélanger
complètement les deux composants. C´est moins évident qu´on ne le penserait dans un système
aussi visqueux ; certains fabricants mélangent un colorant à leur catalyseur, pour permettre à
l´amateur d´évaluer la qualité du mélangeage : c´est fini quand la couleur
est parfaitement homogène.
3 Éliminer les bulles
au maximum. La méthode minimaliste consiste à laisser reposer un peu le silicone avant coulée. Mieux
que rien, mais pas très efficace. La méthode idéale consiste à mettre la résine sous
vide à ce stade. C´est une question de matériel (pompe et enceinte à vide) et c´est coûteux
à moins d´avoir accès à un laboratoire de chimie.... La voie moyenne consiste à
centrifuger le mélange, en attachant le récipient qui le contient au bout d´une ficelle que l´on
fait tournoyer à grande vitesse comme une fronde. C´est assez efficace, mais bonjour les dégâts
si on lâche la ficelle ! A faire absolument à l´extérieur.
4 Être patient...
Encore plus patient ! Le caoutchouc paraît solidifié après quelques heures, au plus tard le lendemain
(sinon, c´est qu´il y a un problème). Mais il n´a pas encore acquis, tant s´en faut, sa
résistance finale. Il lui faudra pour cela près d´une semaine. Donc attendre. On peut accélérer
et même améliorer le résultat final en chauffant le moule vers 40 ou 50 degrés, si les matériaux
du modèle maître le permettent (attention à la Plasticine !).
 |
La conception et la fabrication du moule |
Comme le montre la photo ci-dessus, le moule est en deux parties.
Une sorte de baignoire qui épouse l´extérieur de la caisse et ses détails, et un
noyau qui forme l´intérieur. La coulée de la résine se fera dans la position représentée
sur la photo, avec le noyau introduit dans la baignoire. Le trou de coulée passe à travers le noyau.
Mais le moule de la baignoire est réalisé dans
la position inverse (c´est-à-dire la machine à l´endroit).
PREMIÈRE ÉTAPE On
fabrique une caissette assez grande pour abriter le modèle entier et réserver un peu d´épaisseur
dans toutes les directions. Dans ce cas-ci, les parois latérales se sont révélées un peu minces,
ce qui m´a plus tard obligé à construire un renfort en carte plastique pour le moule. Je réalise
d´habitude ce moule du moule en carte plastique, mais le bois ou le carton fort peuvent convenir si leur
porosité est scellée, par exemple à la cire.
DEUXIÈME ÉTAPE L´intérieur
de la caisse du modèle maître est rempli de pâte à modeler. De cette façon, le silicone
ne pourra pas y pénétrer. La locomotive doit reposer sur un socle de Plasticine, de manière à
rester bien verticale, toit en l´air, dans le moule du moule.
TROISIÈME ÉTAPE On
prépare le caoutchouc comme décrit précédemment, et on peint d´abord une couche assez
mince de caoutchouc liquide sur toute la surface extérieure de la caisse. Cette façon de procéder
diminue la probabilité de piéger des bulles sur la surface du modèle, et permet aussi de voir et de
déloger ou éclater celles qui se formeraient. Un cure-dent est très utile pour ce faire.
Le reste du caoutchouc est alors coulé jusqu´à
recouvrir complètement le modèle, plus une surépaisseur d´un centimètre au moins qui
constituera le fond du moule. On laisse prendre complètement (voir ci-dessus).
QUATRIÈME ÉTAPE On
démoule le moule sans toucher au modèle-maître. Ce dernier doit impérativement rester en place,
car, une fois sorti, il n´acceptera plus jamais de retourner en place. On enlève complètement la pâte
à modeler qui remplissait la cavité de la caisse de la loco. Notons au passage que, dans le cas d´une
pièce pleine en moule unique ouvert, le travail de fabrication serait terminé.
CINQUIÈME ÉTAPE Le
demi-moule est replacé dans la caissette (moule du moule), mais dans la position inverse, ventre en l´air.
Sur les bords de la caisse, on colle verticalement, de loin en loin, mais surtout sur les points les plus élevés
de la jupe, des bâtonnets (allumettes) qui serviront à réserver les futurs évents
Une baguette de plus fort diamètre est également
collée verticalement au fond de la caisse (l´envers du toit). Son empreinte servira de trou de coulée
pour la résine lorsque le moule sera en opération.
SIXIÈME ÉTAPE quelques
détrompeurs sont découpés au cutter dans la marge supérieure du demi-moule. Ces petites indentations
serviront à assurer le repositionnement correct des deux parties du moule fini.
Un agent de démoulage (paraffine liquide, spécialité
téflonnée, cire liquide...) est appliqué très soigneusement sur toute la surface visible du
demi-moule (sa margelle). Faute de cette précaution, les deux parties du moule risquent fort de se souder
l´une à l´autre irréversiblement ; Attention ! les agents de démoulage et les
cires au silicone ne conviennent pas, puisqu´elles sont compatibles avec le caoutchouc.
SEPTIÈME ÉTAPE La
caisse est remplie de caoutchouc préparé, comme au point trois 3. Un à deux centimètres
de surépaisseur sont de nouveau nécessaires.
On attend que le caoutchouc acquière toute sa résistance.
Oui, je sais, c´est dur ;¬) C´est alors que vient le moment de séparer les deux parties du
moule et de démouler le modèle maître, ainsi que les bâtonnets et autre baguette.
 |
 |
 |
 |
 |
|
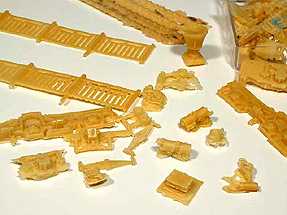 |
|
Des pièces de superdétaillage
pour véhicules et bâtiments.
Une Type 12 belge
agrémentée de pièces en résine.
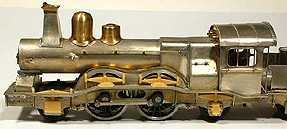 |
|
 |
 |
 |
 |
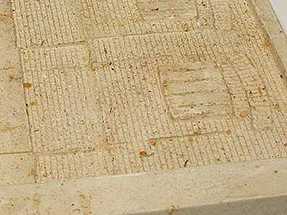 |
Le moule pour des murs, portes et fenêtres... |
 |
La résine : choix et préparation |
Le choix de la résine est important. Le moulage dans
le moule décrit plus haut se fait par gravité, et la résine doit être assez fluide pour remplir
rapidement tout le moule sans laisser de bulles. Elle ne doit pas non plus prendre trop vite, pour la même raison.
Une résine qui devient sirupeuse est perdue pour la coulée.
Celle que j´ai utilisée dans l´exemple illustré
est une résine époxy. Elle est sans charges (comme toutes les résines assez fluides) et très
liquide.
Il existe trois types principaux de résine : époxy,
polyuréthane et polyester ; La dernière est à proscrire, parce que beaucoup trop cassante après
prise, pour le genre d´usage dont nous parlons ici. De plus, elle vieillit mal.
Et c´est dommage, car elle est bon marché et presque
inoffensive pour le caoutchouc du moule.
Les deux autres sont assez similaires entre elles. Les polyuréthane
sont un peu plus robustes mécaniquement, mais j´ignore s´il en existe des variétés suffisamment
liquides.
Un bon mélange en proportions correctes est, rappelons-le,
une nécessité. Lors de la prise, le mélange s´échauffe de manière importante,
et cela accélère la réaction : il s´agit donc d´une réaction en chaîne,
susceptible de s´emballer. Par conséquent, il est prudent d´effectuer son mélange dans un récipient
assez large, où la résine ne se réchauffe pas trop vite parce que la déperdition de chaleur
est suffisante. Inutile pour les petites quantités, cette précaution devient indispensable si on prépare
quelques centaines de grammes de résine.
Avant la première coulée, il faudra estimer le
volume de résine nécessaire pour rempli généreusement le moule. C´est facile, en remplissant
le moule réassemblé, avec de l´eau dont on mesure ensuite le volume.
La résine doit être dé-bullée,
exactement comme le caoutchouc, et les mêmes trucs sont utilisables. Pour être franc, un système à
vide est presque nécessaire pour obtenir un bon résultat, mais le truc de la ficelle est acceptable, à
condition d´opérer vite.
 |
La coulée |
Le moule est réassemblé et maintenu fermé
au moyen de bandes élastiques. Celles-ci ne doivent pas être serrées au point de déformer le
moule. La résine doit être coulée en un seul jet, de manière à ne pas entraîner
de nouvelles bulles par le trou de coulée. Le liquide pénètre au point le plus bas du moule et remonte
le long des parois de la caisse en chassant l´air devant lui ; lorsque la résine déborde par les
évents, la coulée est finie. Recommencez à respirer :¬)))
Pour effectuer la coulée en une fois, il est indispensable
de munir le trou de coulée d´un entonnoir, qui contiendra temporairement l´excédent de résine.
Contrairement au caoutchouc silicone, la résine peut
et doit être démoulée dès que possible. Si la caisse est encore légèrement flexible
au démoulage, ce n´en sera que mieux. Toute déformation raisonnable induite à ce stade sera
spontanément réversible. Il vaut tout de même mieux stocker le modèle, jusqu´à
prise complète, dans une position où il ne se déformera pas sous son propre poids.
La prise, ici également, peut être activée
par un appoint de chaleur.
 |
Les finitions |
Il faudra naturellement araser les colonnettes de résine
correspondant au trou de coulée et aux évents. Sans doute y aura-t-il quelques bulles, des traces de jonction
de moule et autres petites imperfections, à corriger par les moyens habituels : limes, papier abrasif et mastic.
Et voilà !
Il peut se faire que les premières coulées ne
soient pas satisfaisantes, par exemple si les évents sont en nombre insuffisant ou mal placés. Dans ce cas,
il faudra modifier le moule en travaillant précautionneusement du cutter. Il est plus facile d´ajouter des
évents que d´en enlever.
 |
Conclusion |
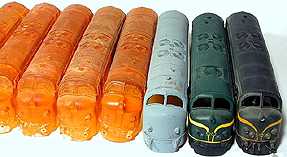 Les
quelques photos jointes montrent la collection de caisses sorties du moule. Toute la production utilisable est dans la
photo ci-contre ; c´est que les moules s´abîment assez rapidement. La résine liquide les
attaque en les fragilisant. Après une à deux douzaines de pièces, la surface du caoutchouc est devenue
cassante, et les pièces suivantes en arrachent des lambeaux lors du démoulage, ce qui ruine évidemment
l´ouvrage.
Sur cette même photo, les deuxième et troisième
locos en partant de la droite ont été modifiées après moulage (respectivement sur la toiture
et sur la face avant). Créer des variantes devient facile à partir d´une caisse en résine.
En bref, si l´entreprise est relativement de longue haleine,
elle n´est nullement impossible. Bonne chance à tous les explorateurs et faites-nous part de vos expériences !
|